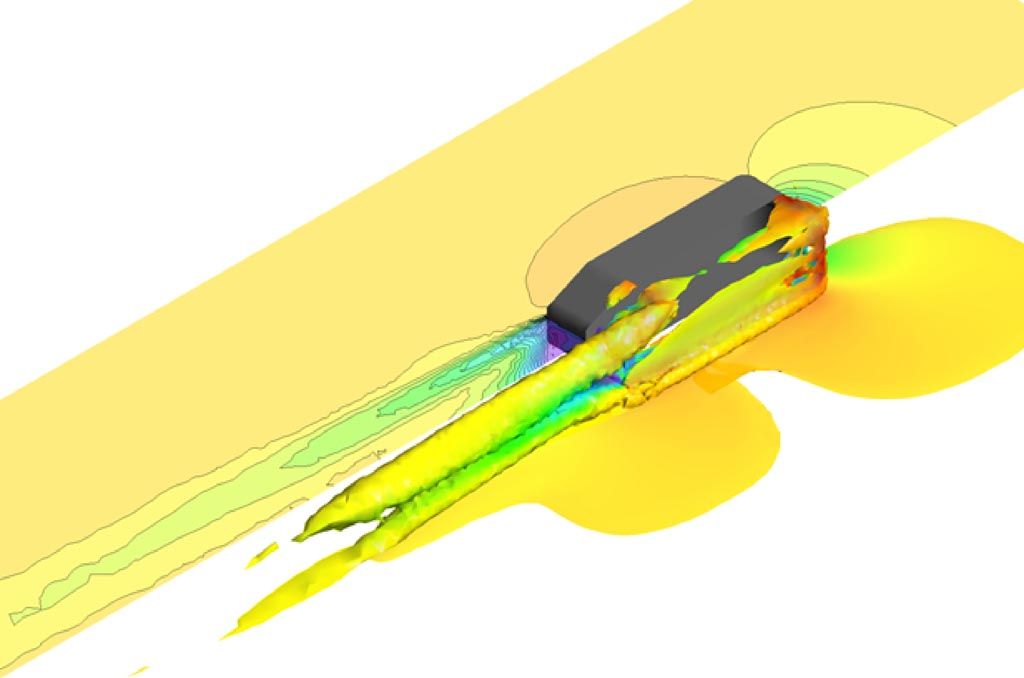
Purpose:
Our diffuser's rear up-turned lip is a bit
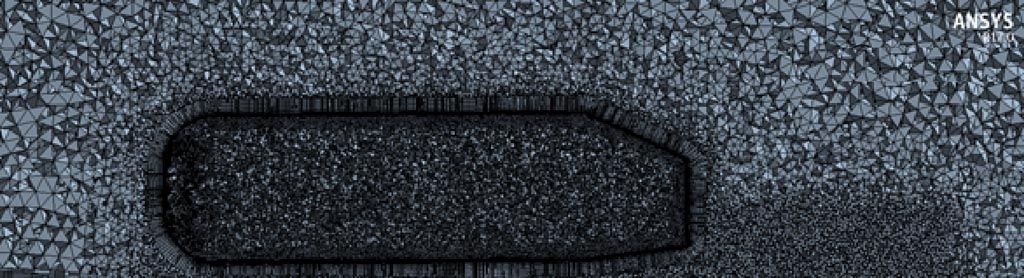
Why was the Ahmed Model Chosen?
The Ahmed model is a universal benchmark used in the automotive field for validating simulation tools. It is also a great model to use for general changes to analyze the effect on a basic vehicle system. Effects on this model likely can transfer to other vehicles, but as always, we recommend and will always perform analysis on vehicle-specific units as each case can vary.
Standard Ahmed Model CFD:
Being that this is an A to B to C comparison, we, of course, have to start with the standard Ahmed model. CFD photos of this are shown below. We took this time to compare the standard Ahmed results to published results as well.
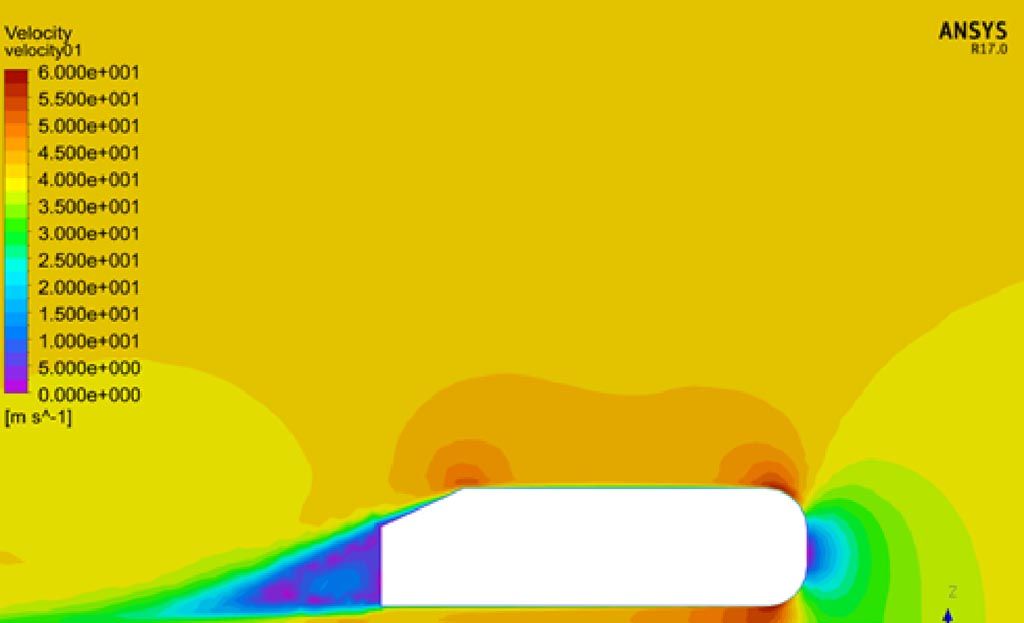
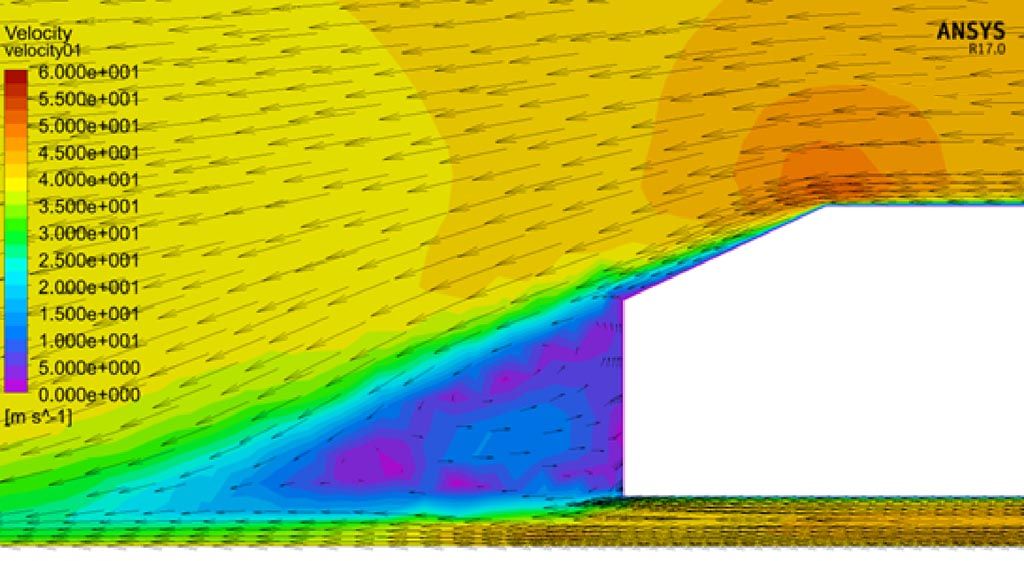
Diffuser Ahmed Models CFD:
We added a diffuser by removing material from the Ahmed model and reran our CFD test. We then added a radius to the rear-most portion of the diffuser to represent a similar up-turned lip to our diffusers. Below are some of the CFD photos.
Velocity Contour Plot:
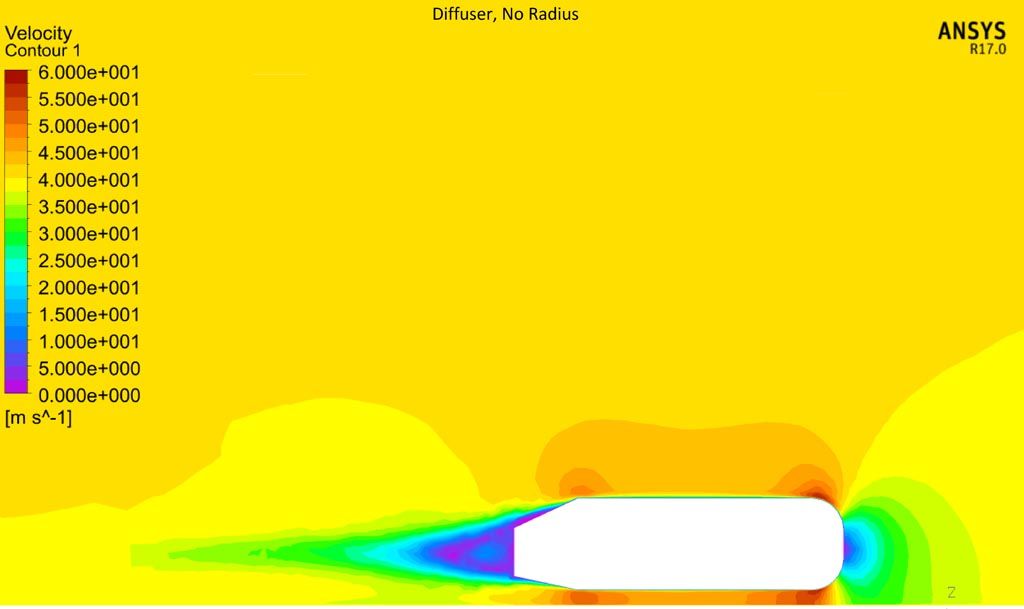
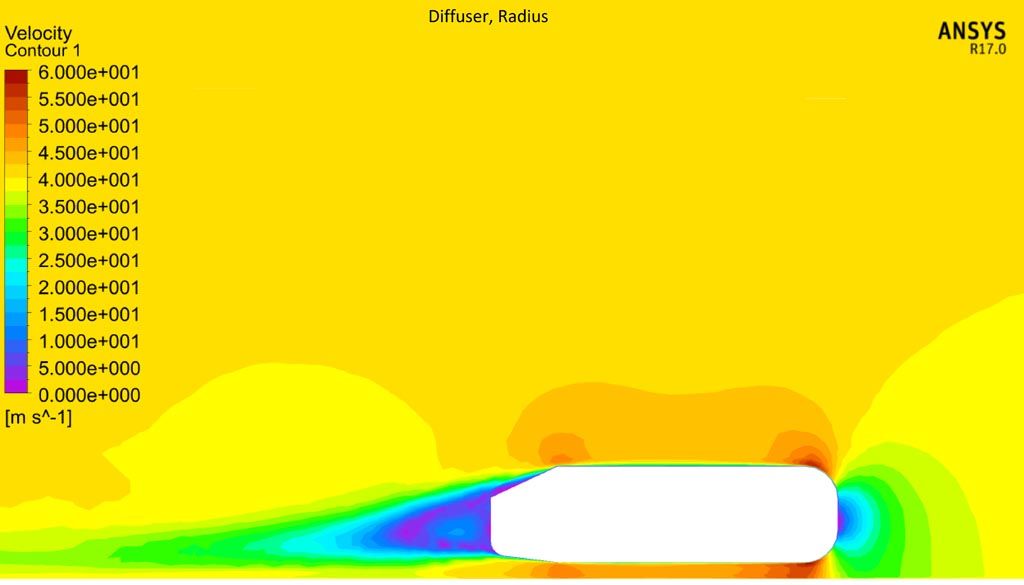
Pressure Contour Plots
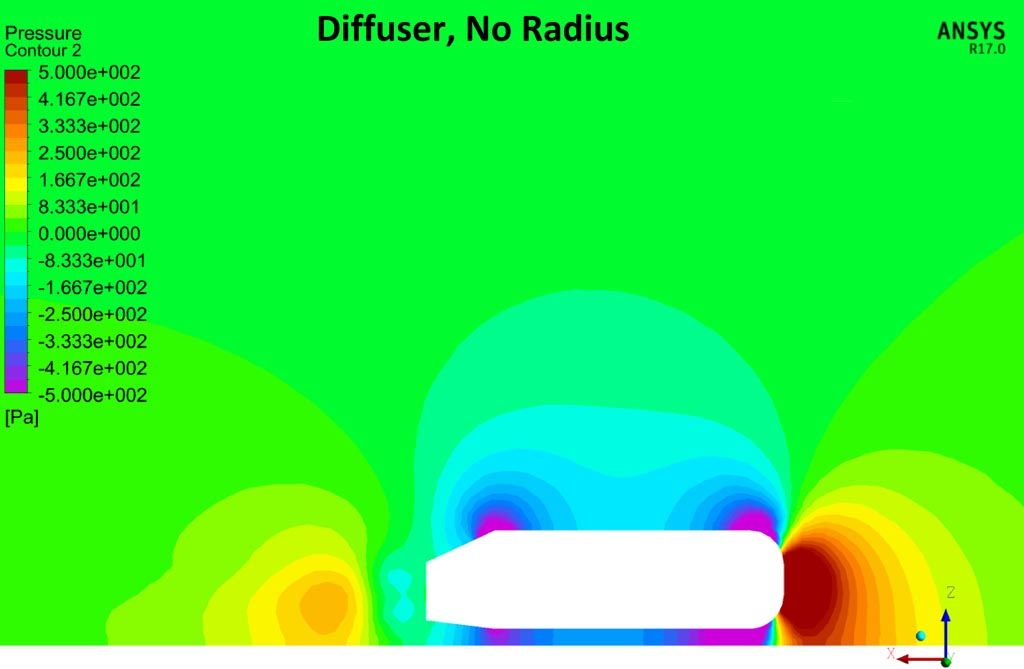
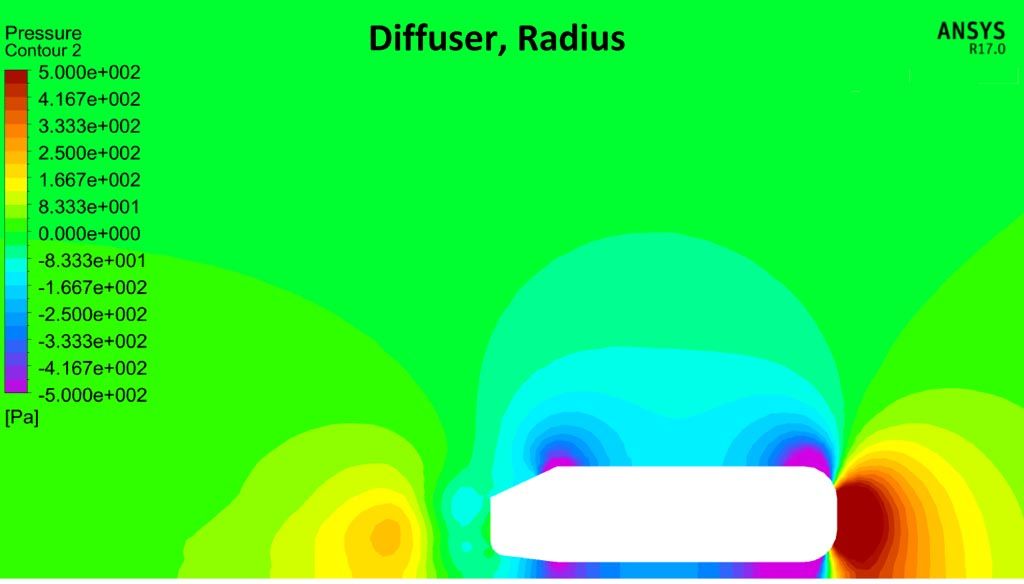
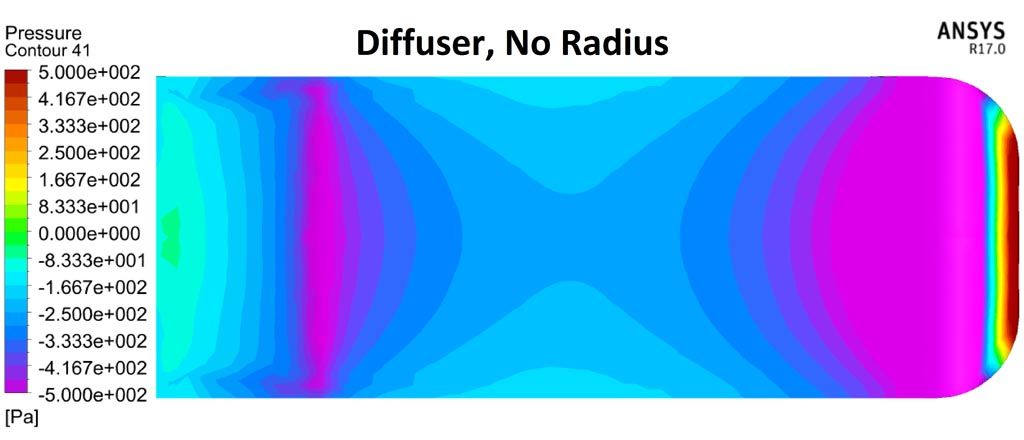
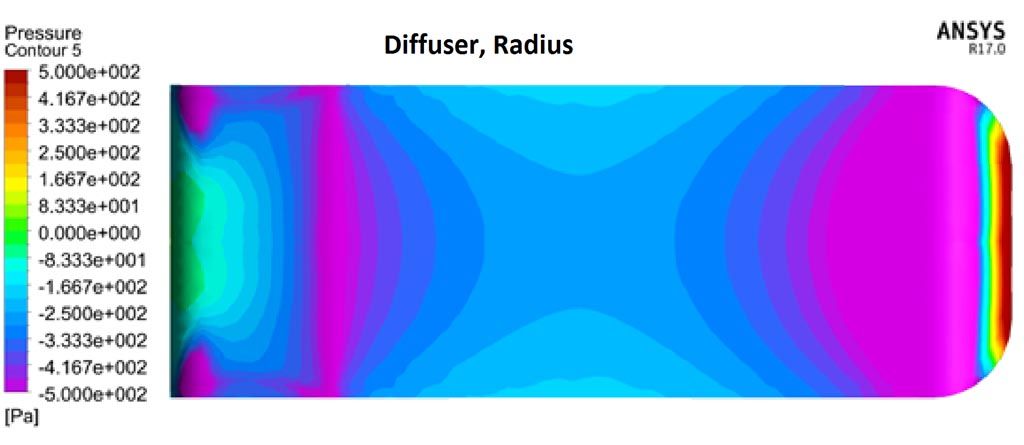
Diffuser Models Numerical Data:
The numerical data speaks volumes. The diffuser with a radius at the end is more efficient. Not only does the
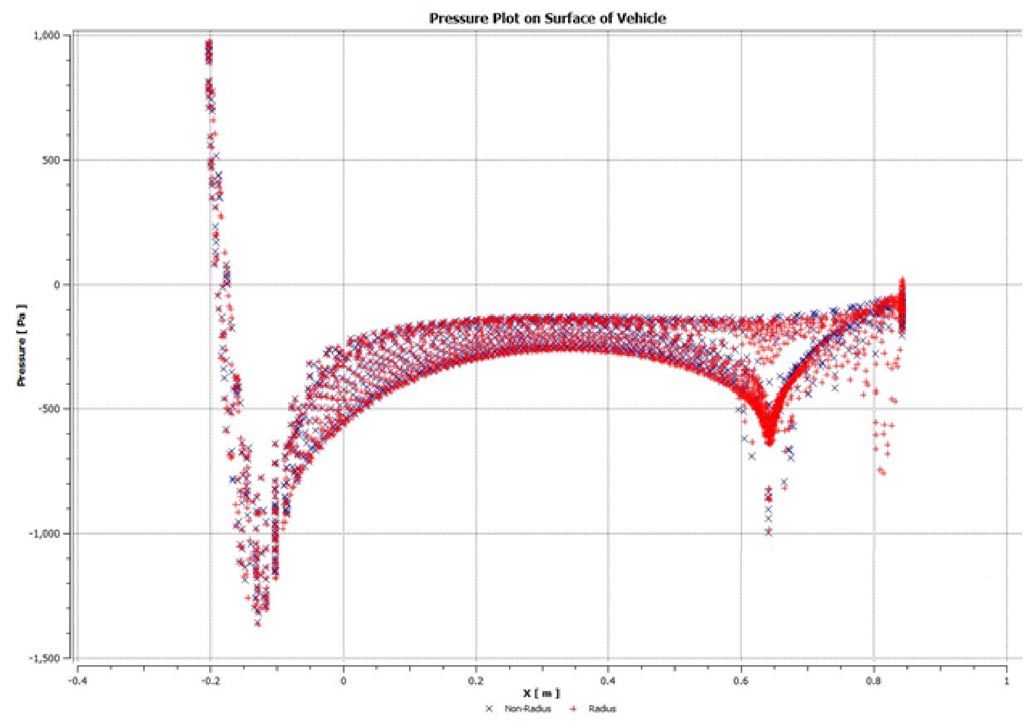

Conclusion:
For this analysis, the radius on the rear of the diffuser makes the vehicle more efficient. This might not always be the case, but this analysis does indicate that the radius on the rear diffuser is not only structurally beneficial but aerodynamically as well. Regardless, we always suggest that all setups should be analyzed and tested before implementation. This is why we CFD test every model and every diffuser we design for optimization.
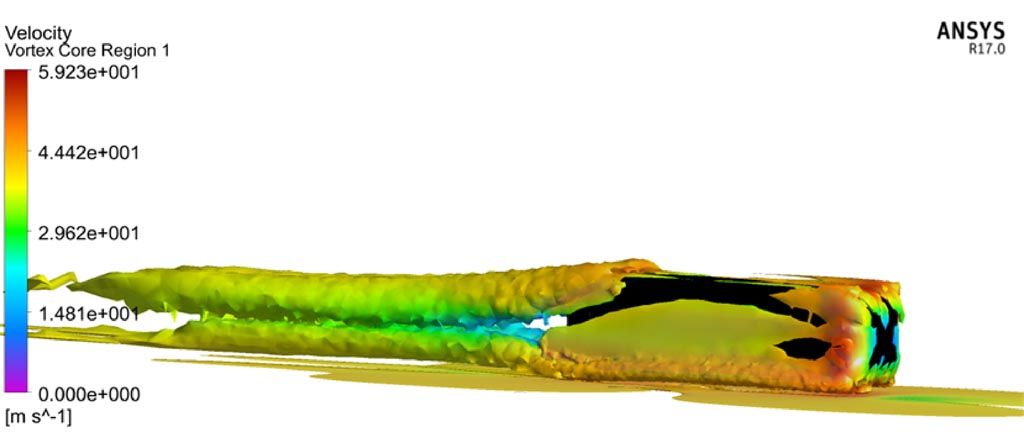
Diffuser Trailing Edge Analysis - Ahmed Model Testing